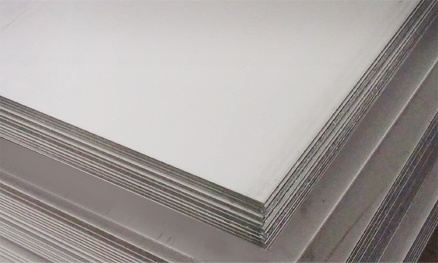
Titanium plate
Products are used in aerospace, aviation, weapons, ships, marine engineering, petrochemical industry, medical health and other related industries. Adopting high quality and sponge titanium as raw materials at home and abroad, strict quality control is carried out from ingot, forging and machining. The product quality is in full compliance with GB/T2965 and ASTMB348 standards.
Titanium rod
Adopting high quality and sponge titanium as raw materials at home and abroad, strict quality control is carried out from ingot, forging and machining. The product quality is in full compliance with GB/T2965 and ASTMB348 standards.
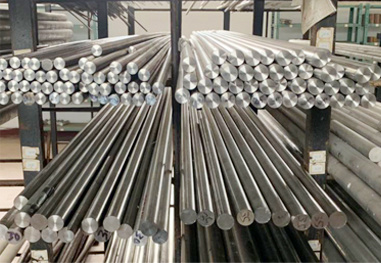
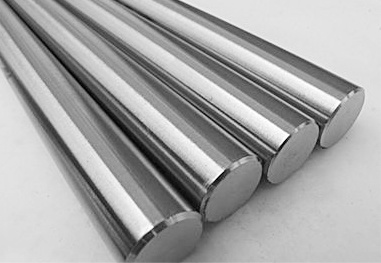
WONDERFUL
— ABOUT US
Yangzhou Wonderful Electromechanical Equipment Complete Engineering Co., Ltd. was established in June 2009 in Yangzhou, a historical and cultural city. In the past 10 years, the company has continued to grow and develop in the spirit of “Made in China is more wonderful than me” and has been recognized and supported by many users. It is the preferred supplier of titanium alloy materials for China Ordnance Group.
PRODUCT CENTER
CREATIVITY LEADS TO QUALITY
WONDERFUL
Market-oriented, technology-oriented, development, quality-oriented, survival, management, efficiency

Advanced Technology
It can produce various specifications of titanium alloy plates, rods and related precision parts.


Management Norms
All employees of the company are united to create a better future!


Security
We are the preferred supplier of titanium alloy materials of China Ordnance Group.


Service Support
We provide customers with professional knowledge, considerate service and perfect after-sales service.

NEWS CENTER